Indonesia Furniture Manufacturers Things To Know Before You Get This
Indonesia Furniture Manufacturers Things To Know Before You Get This
Blog Article
Fascination About Indonesia Furniture Manufacturers
Table of ContentsThe Single Strategy To Use For Indonesia Furniture Manufacturers4 Easy Facts About Indonesia Furniture Manufacturers Explained3 Easy Facts About Indonesia Furniture Manufacturers ExplainedSome Known Factual Statements About Indonesia Furniture Manufacturers Not known Facts About Indonesia Furniture Manufacturers
There are some drawbacks to purchasing from a furnishings maker. A furnishings merchant is a business that markets furnishings made by numerous suppliers.When you acquire from a furnishings merchant, you're getting a furniture that's currently been made and prepares to be delivered to your home. Among the advantages of buying from a furnishings retailer is that you can often see and touch the product before you purchase it.
At BH Furniture, our team believe in establishing new criteria for quality in the production of commercial furnishings - Indonesia furniture manufacturers. Our commitment to innovation has actually led us to accept advanced automation technology, changing the way we make furniture and moving us to the center of the market. Gone are the days of manual labor controling the production flooring
Our equipment works effortlessly, guided by the exact criteria established by our competent designers, making sure consistently top notch outcome. Bid farewell to production hold-ups and overtime expenses. Our automated systems operate tirelessly, 24/7, guaranteeing a consistent and undisturbed operations. This implies we not just fulfill but exceed shipment target dates, providing our clients with a level of dependability that traditional production techniques merely can't match.
The Main Principles Of Indonesia Furniture Manufacturers
Our manufacturing ability has skyrocketed, enabling us to satisfy the demands of even the largest projects without compromising on high quality. As your companion in business furnishings remedies, we can easily scale our result to accommodate your requirements, no matter the range. While standard production counts heavily on hand-operated labor, our automated systems have substantially lowered our dependancy on a big labor force.
Furnishings production is an intricate procedure that includes numerous phases, from designing and product choice to production and setting up. At each stage, there is an opportunity of problems or mistakes that can jeopardize the quality of the last item. To make sure that furniture is of top quality, furniture producers carry out quality control procedures to determine and rectify any type of problems that may arise throughout production.
The assessment process must cover different facets, such as assembly, surface, colour, layout, packaging, labelling, and noting. By implementing an extensive inspection process, manufacturers can ensure their items fulfill the essential quality, security, and sturdiness needs. They also supply the adaptability to address problems and make improvements before completing the last item.
Furnishings quality standards are sets of guidelines and demands for furniture manufacturing. They define the needed high quality level of furniture manufacturing and cover elements such as safety, sturdiness, toughness, about his and ecological check this impact.
An Unbiased View of Indonesia Furniture Manufacturers

To ensure their furniture items can endure different weather aspects, including sun, rainfall, snow, and wind, suppliers should think about internationally identified standards that comprise examinations and testing. Below are some of the criteria to bear in mind: ASTM F1561-03 is an international standard established by the American Section of the International Organization for Testing Products (ASTM).
UL 962 is a worldwide safety and security criterion developed by Underwriters Laboratories (UL), an independent worldwide supply safety and security solutions business. The standard applies company website to family and business home furnishings, including outside furnishings.

The 5-Second Trick For Indonesia Furniture Manufacturers
It assists to determine issues in the furnishings and evaluate its performance and compliance with the needed high quality criteria. Below are the steps for carrying out lab testing for furnishings: Makers accumulate examples of furnishings elements that need screening. These examples commonly stand for the various sorts of furnishings that they generate.
This may involve a mix of various examinations, including stamina testing, sturdiness testing, safety testing, and ecological effect testing. The samples are after that checked for different high quality parameters, such as toughness, longevity, safety and security, and environmental impact. The outcomes are after that assessed to determine whether the items satisfy the required top quality criteria.
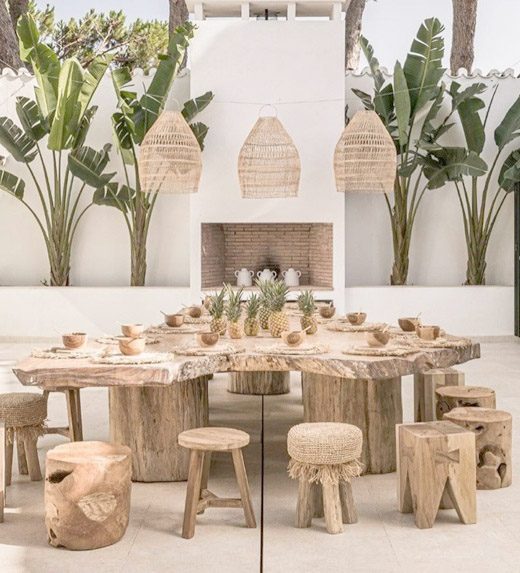
Typically, every store furnishings is different. All projects have regarding a month's time in between layout ideation and final manufacturing. This is where the major obstacle exists. Layouts meeting client convenience Optimizing space usage in storage, screen, tramp, visitor seats and walkways Making sure convenience of access to products for trials and purchase Designing modular furniture that is simple to relocate and renovate Fulfilling safety and security needs of customers A quick TAT from design to manufacturing and setup with marginal mistakes can aid resolve the above concerns.
The 8-Minute Rule for Indonesia Furniture Manufacturers
Also, a developer can comprehend the marketplace patterns and prepare with ingenious layouts beforehand. Check out here: Just How DriveWorks Helps You to Reduce Preparation in Manufacturing Developers commonly have to transform the sizes and shapes of furniture at a minute's notification. These might have various aesthetic and useful demands like front workdesk, and servicing workdesk that vary in measurements.
Improves item quality and minimizes scrap. Field guideline files along with amount departures are also created for retail shop furnishings installations. Style iterations and disputes are reduced, and the store flooring can start making on the day of sales.
It is a highly competitive market, with services making every effort to keep up with altering customer demands and the newest technical trends. Today's consumers are a lot more most likely to prefer furniture that is customized and made with sustainable products.
Report this page